Pharmaceutical Bottle Packaging: 3 Essential Features for Safety
Miscounted bottles? Cracked tablets?
In the world of pharmaceutical bottle packaging, quality assurance couldn’t be more important.
Pharmaceutical bottle packaging packaging doesn’t just store and transport medication. Packaging service providers play an essential role in the safety and security of these products by packaging doses accurately and efficiently. It’s crucial to work with a pharmaceutical bottle packaging company that understands the importance of these features and can provide tailored solutions to meet changing needs.
That’s why we invested in an Uhlmann IBC 150 Monoblock Bottling Unit with integrated cartoning and bundling – to enhance our solid-dose bottle packaging services with serialization in a few essential ways.
Let’s explore the top three features that enhance pharmaceutical bottle packaging solutions:
- Accuracy
- Versatility
- Production Efficiency
Accurate Pharmaceutical Bottle Packaging for Solid Oral Dosage Forms
Accuracy can make or break your product.
What happens if your pharmaceutical product is packaged incorrectly? Your consumers lose trust in you, your product, and your brand. If it’s a prescription drug, miscounted or damaged product can compromise patient safety. Accurate bottle packaging services protect your product, your brand, and your consumers.
Uhlmann’s IBC 150 uses industry-leading Cremer technology to count and package solid oral dose products, including tablets, soft gels, and hard gels. Counting over 18,000 tablets per minute, this infrared technology visually counts every single tablet, no matter its shape, size, color, or clarity. No underfills, no overfills.
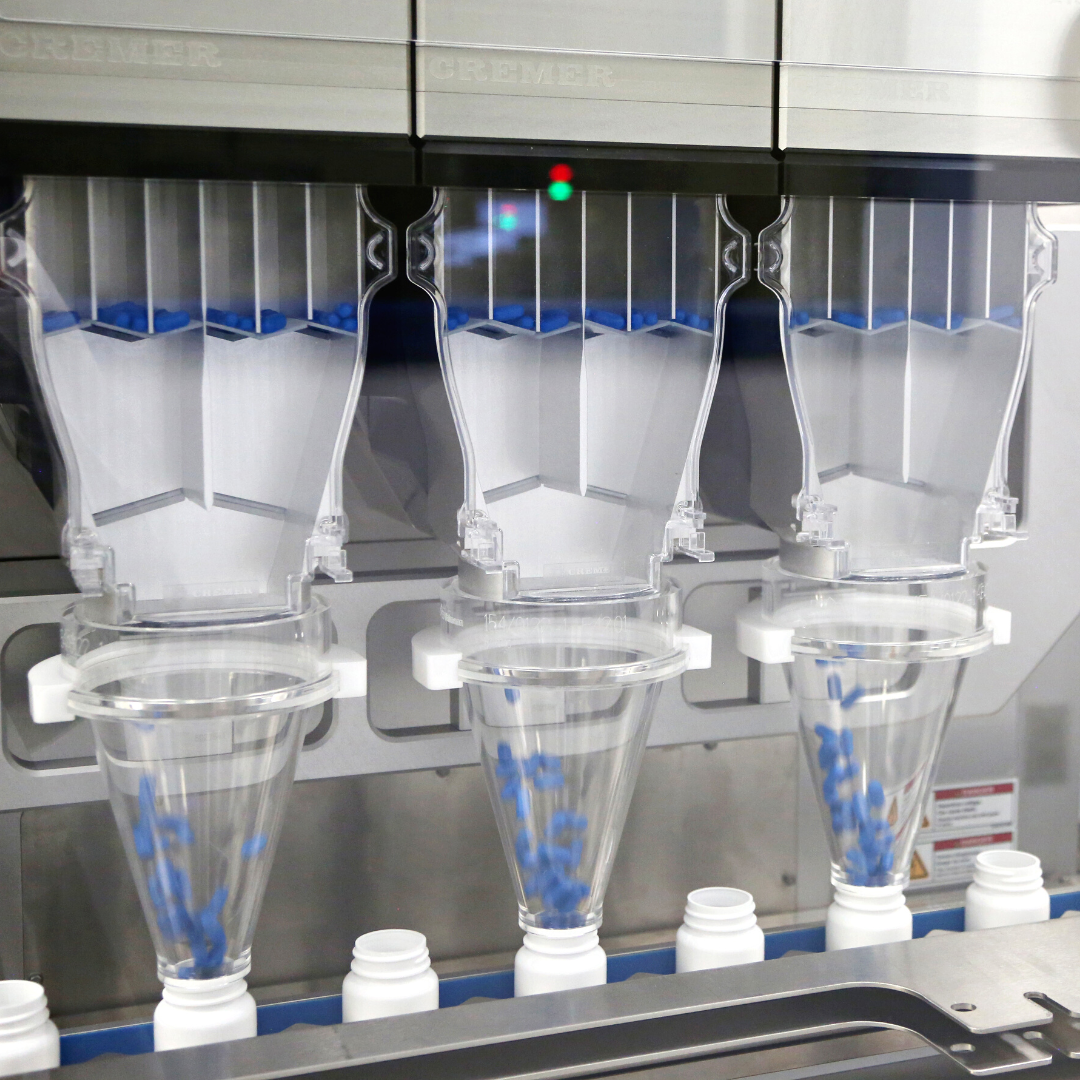
Precision in Healthcare: The Uhlmann IBC 150 CREMER Pharmaceutical Bottle Packaging Machine Efficiently Sorts and Dispenses Blue Capsules into Bottles for Distribution.
A thorough inspection and rejection system minimizes wasted materials. If it does detect an incorrect count at any point in the line, the bottle will be rejected, and no other packaging components will be added along the line. Highly accurate bottle packaging maximizes a packager’s use of bulk products with fewer rejects, leading to an efficient and productive operation.
The Role of Advanced Pharmaceutical Bottle Packaging in Patient Safety
Beyond efficiency, precise packaging prioritizes the safety and health of patients and consumers.
Miscounted tablets or pills in a bottle can compromise patient safety and treatment outcomes and lead to costly product recalls.
Alongside patient health and safety, accurate counting is important from a regulatory standpoint in both the United States and Canada. Medications must be labelled with correct dosage information and the number of pills or tablets in each bottle. Errors can damage the manufacturer’s reputation and lead to financial and legal penalties.
Harnessing Versatility in Pharmaceutical Bottle Packaging
Manufacturers can achieve accuracy and still miss the mark. That’s where versatility comes in.
Versatile bottle packaging equipment is essential for those who support a diverse range of prescription drug medication and over-the-counter products, like contract packagers.
Adapting to Diverse Needs with Advanced Bottle Packaging Equipment
The Uhlmann IBC 150 bottling line is a great example of this. As a highly versatile machine, it can accommodate a wide range of products including tablets and pills of different shapes and sizes, various types of bottles, cotton inserts, desiccants, and caps. With this vast range, packaging suppliers can easily run diverse projects through the same bottling machine with quick changeovers for enhanced speed to market for clients.
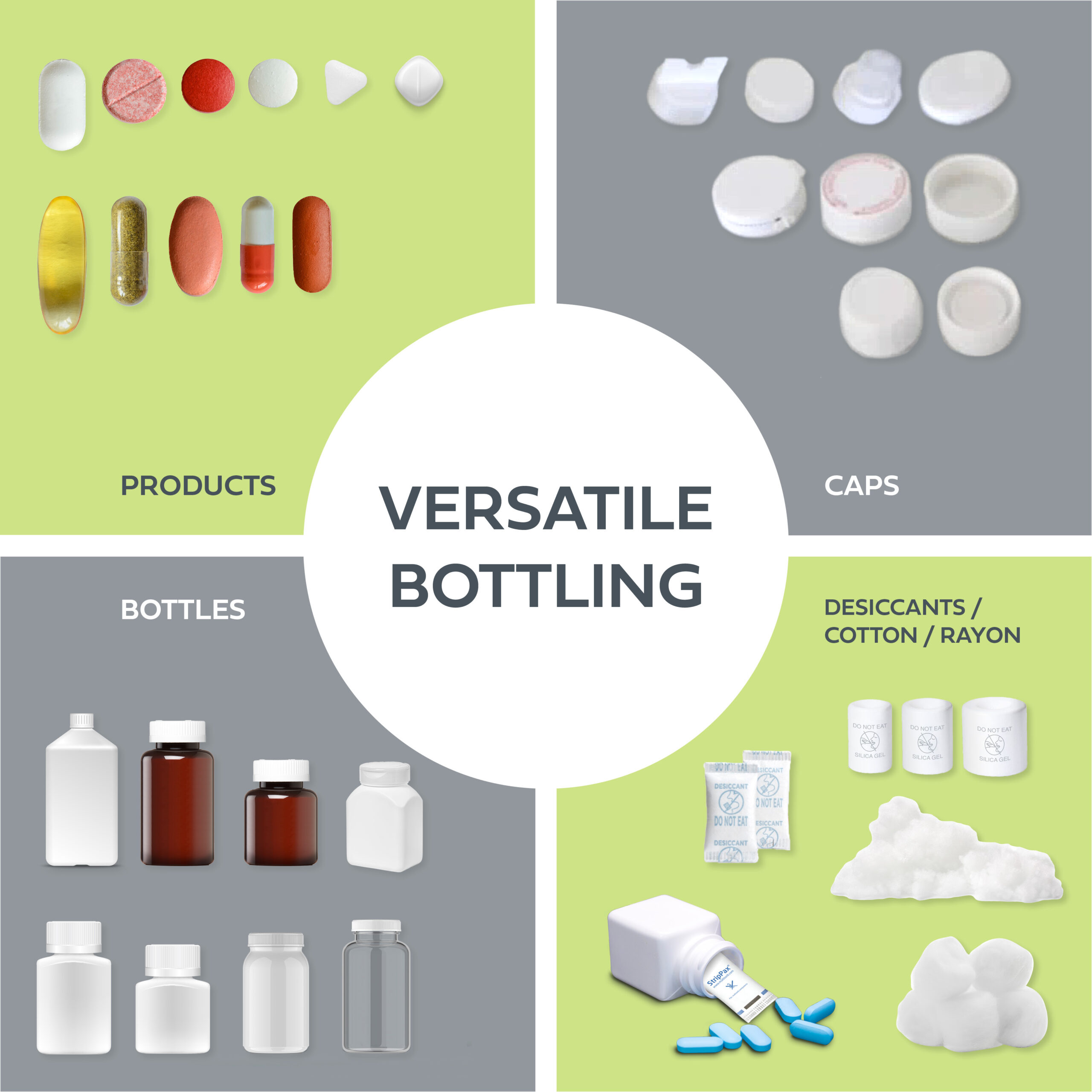
Comprehensive Components of Pharmaceutical Bottle Packaging – From Varied Medication Forms to Diverse Bottling Solutions, Highlighting the Industry’s Capacity for Versatile Bottling.
Versatility can make all the difference with evolving regulations and changing market demands, helping to adapt to new trends. Versatile equipment, responsive service and significant experience in pharmaceutical packaging become the real superstars when pharmaceutical brands need to develop packaging solutions for new products.
Whether it’s a new product launching to market or an existing product, packagers with versatile equipment can achieve their clients’ packaging needs, regardless of their unique requirements.
Production Efficiency in Pharmaceutical Packaging
Pharmaceutical packaging suppliers need to be responsive, nimble, and agile in today’s competitive marketplace. That’s why it’s important to have integrated equipment that fulfills many functions to drive speed and efficiency.
The Uhlmann IBC 150 bottling line is a game-changer for pharmaceutical packaging since it combines four machines into one footprint, including desiccant feeding, counting and feeding, cotton/rayon insertion, and capping machines to support the primary packaging process.
Our line is also equipped with cartoning and bundling capabilities to support the secondary packaging process, plus a secure serialization platform compliant with the Drug Supply Chain and Security Act (DSCA) for prescription pharmaceutical products.
The result: market-ready products packaged with accuracy on one packaging line.
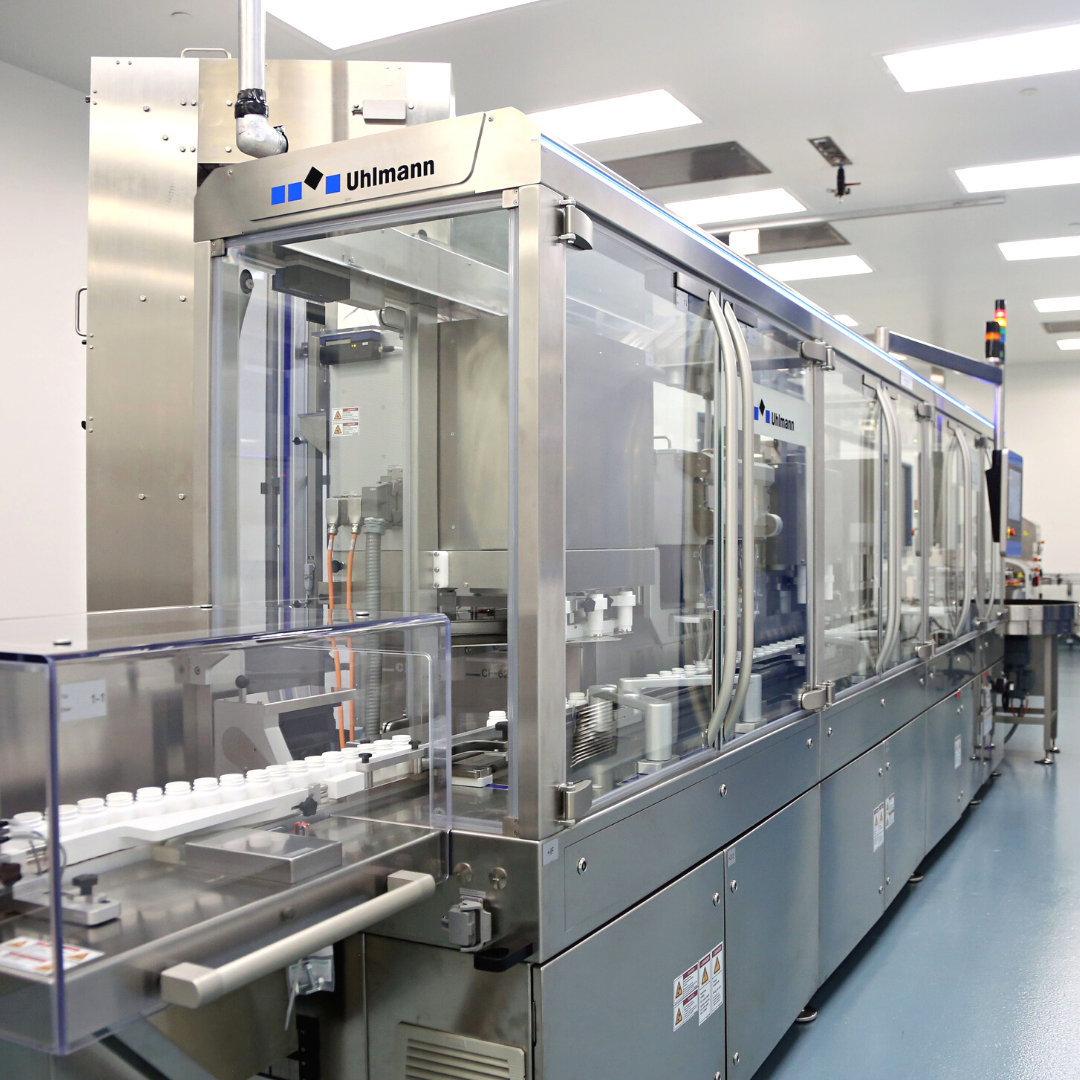
Streamlining Efficiency: The Uhlmann IBC 150 Pharmaceutical Bottle Packaging Machine, a Beacon of Modern Automation in Medication Packaging Processes.
Integrating Innovation for Enhanced Packaging Speed and Agility
Unlike traditional bottle lines, this unique integrated Uhlmann line design ensures all steps in the packaging process work in unison. There is no need to ramp up separate machines to top speed, which results in faster set-up times overall.
By effectively prioritizing resources, pharmaceutical packaging providers like Jones Healthcare Group can concentrate on delivering the best possible product for their clients. Backed by these three pillars of accuracy, versatility, and production efficiency, we can deliver high-quality products and services every time.
For more on our range of filling services and how we can advance your business, visit our packaging services page.