A Dynamic Packaging Launch Is More Like Rocket Science Than You Might Think
A new framework for space exploration has emerged in recent years, one that includes global partnerships and cooperation between government and commercial entities. This has reignited the general public’s interest in all things space.
Navigating the Complexities of a Pharmaceutical Packaging Launch
While most of us have a limited understanding of space operations, who among us doesn’t stop what we’re doing to watch a rocket launch when broadcast on the news? They are exciting and cause us to say, “Wow!” They are also complex and require the efforts of thousands of scientists and engineers working together with no room for error. According to NASA, 90% of their staff’s time is devoted to planning, organizing, training and education, and only 10% to controlling missions.1
I am not trying to convince you that commercial drug packaging is as complex as a rocket launch, but there are similarities. Using the right framework and devoting the right amount of time and resources to planning and organizing are necessary for a successful commercial packaging launch, including the “wow factor.”
Building a Customer-Centric Foundation in Contract Packaging
Establishing a Customer-Centred Framework
As a contract packaging organization, being customer-centred is essential and the framework begins the moment we first interact with a customer. During these first meetings, we embark on a process to fully understand and document client expectations, drug specifications, packaging launch requirements, market forecasts and technical specifications.
In its simplest form, being customer-centred means knowing what needs to be done and when. Inside the “what and when” lies a myriad of details and the packaging service provider, who is intimately familiar with their own capabilities, must identify the critical tasks necessary for the client to effectively achieve their deliverables and build the project plan.
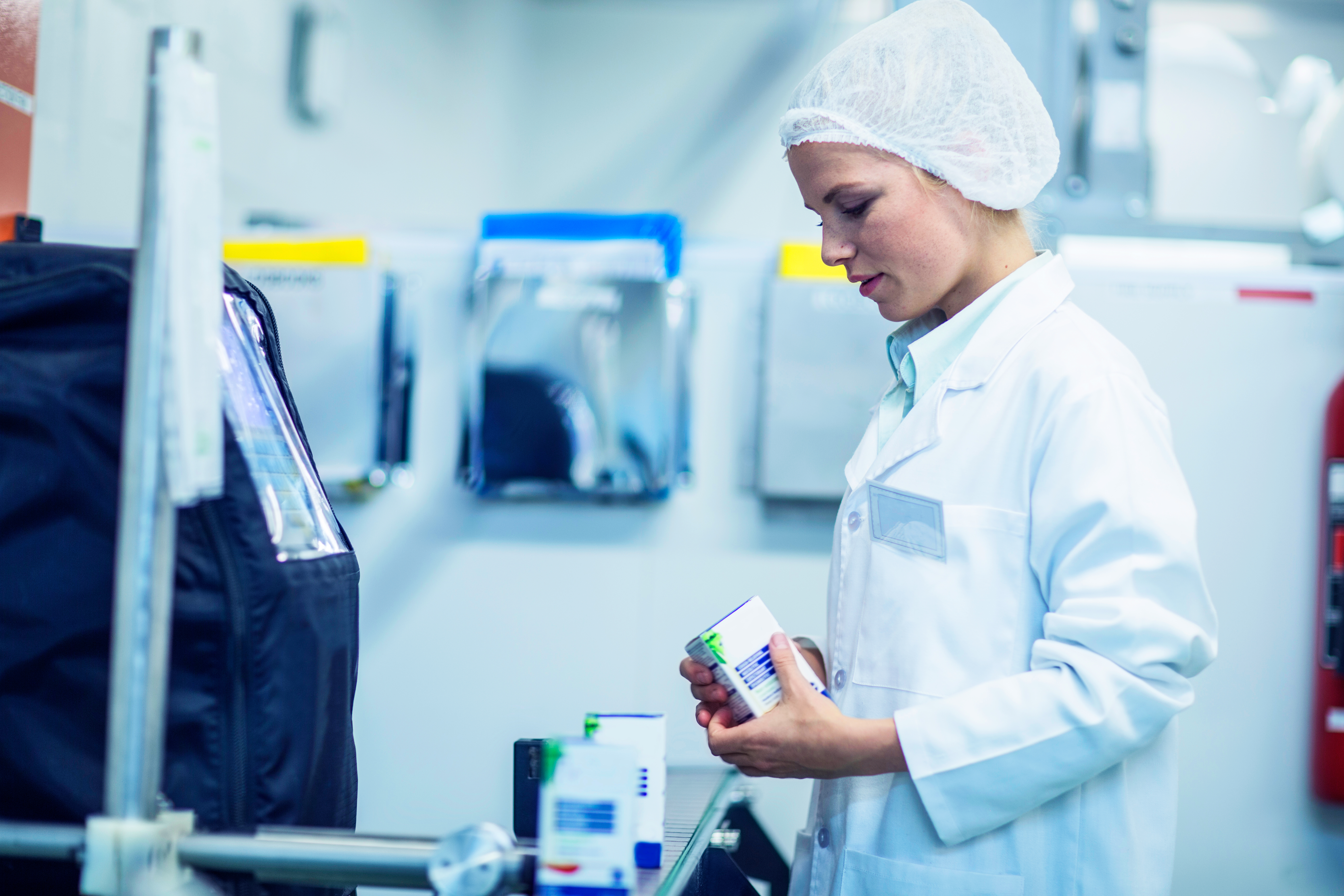
Dedicated to Excellence: A Specialist Prepares for a Pharmaceutical Packaging Launch, Guaranteeing the Highest Standards in Product Safety.
While overall customer deliverables do not often change significantly, projects do, and flexibility is an important aspect of being customer-centred. Project changes can happen for a variety of reasons—patient needs, refined demand forecasting, market conditions, and global events that impact supply chains, such as the current COVID-19 pandemic. Being open to, and expecting, change is the best way to serve the pharmaceutical company, patients, and the healthcare system we collectively support.
The foundation for the pharmaceutical industry is quality and that includes drug product packaging. Drug therapies must be packaged and delivered to the patient with their intended efficacy. Each drug product has critical quality attributes (CQAs) and so does the packaging launch process and package itself. The package and process must therefore be developed with the same due diligence and quality assurance as the drug product.
Packaging and process requirements are identified early in the project, ensuring any required engineering and packaging line trials are completed on time. This will ensure package quality, functionality and integrity is properly achieved. It is important that teams from the client and the service provider meet to review these CQAs to ensure alignment as part of the technical transfer.
A customer-centred framework is essential in packaging launching and executing commercial projects to achieve success. The framework includes fully understanding the customer’s deliverables, expecting change management, being agile, clearly identifying and meeting the packaging CQAs.
Enhancing Communication and Efficiency in Packaging Launch Operations
Communications
Effective communications across the functional areas within the service provider organization, as well as between the service provider and pharmaceutical client are critical. To ensure effectiveness, communications must be planned and intentional, while still allowing agility to escalate issues as required.
Project managers and teams for both parties should be clearly identified with contact information disseminated. Parties should agree upon a formal meeting cadence and reporting structure. A shared and agreed upon project timeline is imperative as it allows critical project points to be identified and the opportunity to mitigate risks proactively.
The written framework that supports these communications will often include the quality agreement, product and packaging launch specifications and meeting minutes, to name a few. Formal project plans, often supported visually with a Gantt chart, are not only significant but also critical in communicating where a project is at all stages during the technical transfer and launch phase.
While this process is heavily regulated, agility from all team members is required. A strong project team with open lines of communication will quickly share any changes that could potentially have an impact on the project scope and/or timing.
Proactive Contingency Planning in a Pharmaceutical Packaging Launch
Spotting irregularities or nuances that may potentially become costly issues or pose a risk to a product launch is invaluable. A knowledgeable workforce, with years of experience, can detect trouble before it becomes a problem.
Drug packaging can be complex and labeling artwork is often intricate, containing detailed, colored brand images, extended content label instructions for patients, and information required by regulatory bodies. For example, track and trace or serialization codes add another layer of potential complexity to prescription pharmaceutical package design. While specific placement is not directed by regulatory authorities, serialization codes must be scanned and stored at the point of packaging.
Experience tells us to conduct adequate test runs before determining the final package layout design. Doing so avoids the costly process of redesigning an entire commercial inventory and the risk of failing to meet project timelines.
Another critical area worth close examination is the service provider’s ability to manage and adjust capacity to ensure meeting the project delivery date. No one wants to have idle packaging lines, but a reasonable amount of capacity available for agility purposes when changes occur is prudent. At Jones, our cross-functional team of skilled operation managers, production team leaders and schedulers work closely together to ensure surge capacity is available for unexpected client needs. As a team, we can synchronize the production of multiple packaging lines so projects are delivered on time and flexibility is maintained for unexpected changes or emergency distribution to overcome critical drug shortages.
Packaging commercial pharmaceuticals products is not technically rocket science, but it is far more complicated than one might assume. Having an experienced and passionate team of professionals will lead to a successful project. Whether drug producers are packaging in-house or using a service provider, success can be achieved by using the right framework.
Begin with a full understanding of the drug organization’s deliverables—what needs to be done and when, document and understand the CQAs, and be flexible by expecting changes. Develop a communications plan that is proactive, intentional and connects the people who can offer solutions to issues. Have proactive contingency plans in place before they become costly problems or pose risks to project timelines.
NASA - The People Behind the Astronauts: https://www.nasa.gov/audience/foreducators/k-4/features/F_People_Behind_the_Astronauts.html